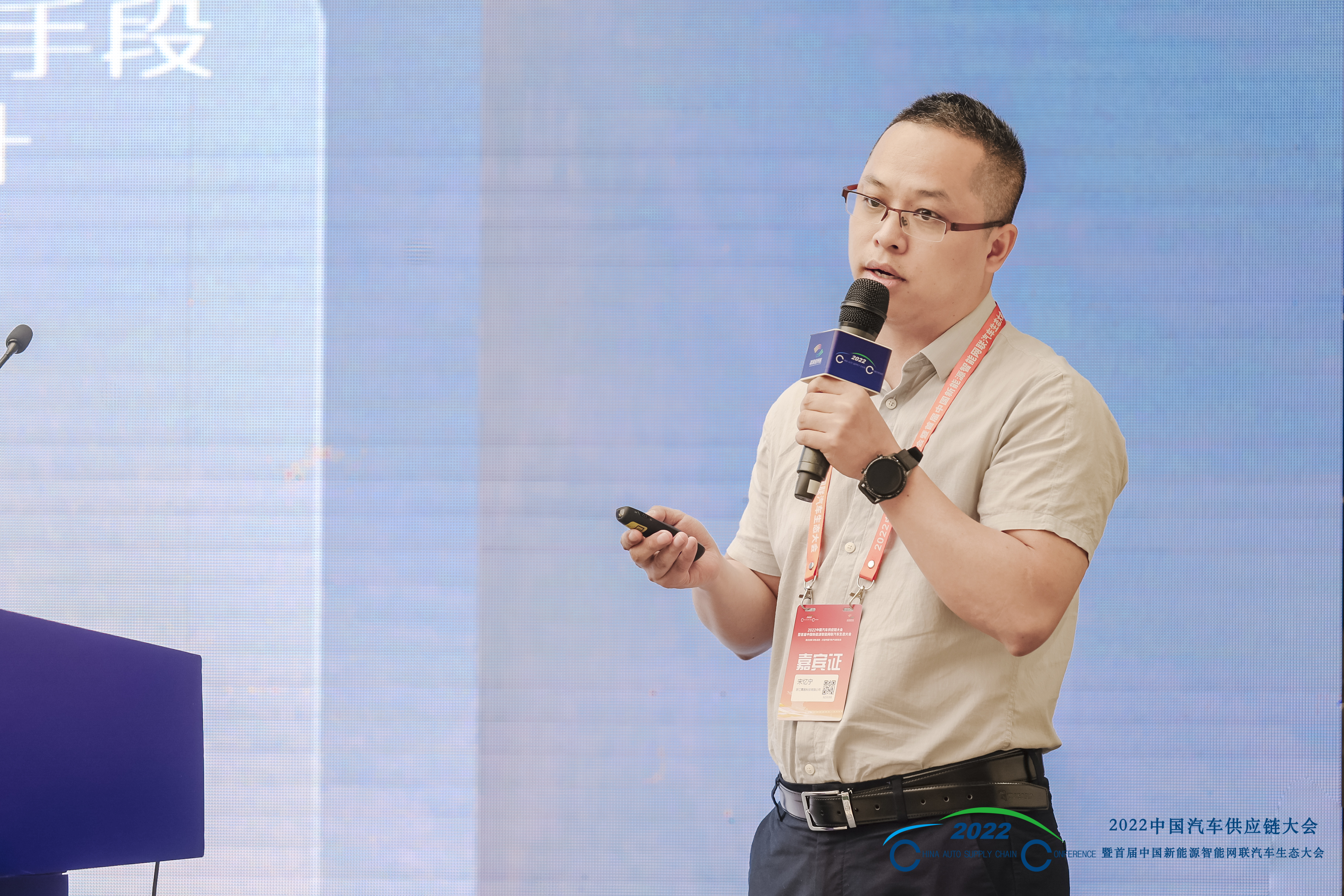
早在2016年,零跑汽车董事长朱江明先生就从智能手机集成式的方式得到了一些灵感,他说既然智能手机能够把电池和手机集成在一起,那我们汽车能不能把电池和车子集成在一起呢?当时朱总提出这个要求的时候,很多人持有怀疑态度,跟我提要求的时候,真的不敢想象。为什么呢?动力电池在车里面应该是它的心脏,我们想要对心脏动手术,这确实是一件不容易的事情。
从动力电池技术发展的角度来讲,当下基本上是两条路线来提升技术,一是材料路线,二是工程路线。材料路线,主要是从物理、化学等学科的突破带来性能的提升。最近几年,特别是中国企业在电芯、正负极材料取得了飞速的发展,导致中国在全球动力电池领域走在前列。但是目前在动力电池没有革命性技术突破和落地的情况下,行业普遍认为只有通过工程技术手段,也就是结构方面去进行提升。我们今天讲的CTC技术,就是通过集成化,给车子做一些提升。
从动力电池系统发展来讲,最近几年动力电池总结为三个阶段,十年以前从德国的标准VDA、MEB,把电芯做成模组,模组做成pack,集成效率不是很高。发现问题的行业专家们开始把模组做大,比如一个模组1.8米或者二三十度电,大家想到把电芯直接集成到pack里面,零跑在2019年已经把CTP应用在车上,目前行业正处于从1.0时代到2.0时代的跨越。还没等2.0阶段全面铺开,大家都忍耐不住了,车的性能要提升,因此零跑在全球首次把CTC技术实现量产装车,首次在C01车型上量产这个技术。我们认为目前的CTC技术,把电池和整车集成,可以被称为3.0时代。从这个角度来讲,零跑汽车应该毫不夸张地说,我们第一家量产,我们也是做勇敢的尝试,所以我们认为零跑引领了CTC技术的发展。
从CTC技术来讲,政府也是大力支持,国务院印发的新能源汽车产业发展规划有提到,研发新一代模块化高性能整车平台,攻关纯电动车底盘一体化设计、多能源动力系统集成技术,包括发改委和国家也在支持三电和整车的集成化。可以说CTC技术是整个电动车行业一次巨大的变革和创新,商业模式和分工协作也将进行颠覆。我为什么讲这个话呢?传统分离式电池包,大部分都是电池厂把电芯做成pack,当然车厂也有自己做pack的,很大部分都是电池厂或者第三方pack厂来主导这个事情。但是今天不好意思,CTC出现以后,必须由车厂主导。为什么?我们做这个事情的时候,16年提出这个概念,18年我们做的时候,当时从整车设计开始四年时间把这个事情做出来。设计车的时候,必须要设计电池,设计电池的时候,每天要跟车在一起,所以我们当时成立一个项目组,有电池,底盘,有车身,有电气。我们认为汽车厂商掌握主导权、定义权,这也是对的,因为汽车是大集成,是终端产品,应该由车厂主导这个事。
零跑汽车全域自研,包括软件、硬件和算法。熟悉我们的人都知道,零跑汽车电池领域从2020年下半年开始,全部是买电芯100%把电芯采购过来自己做成BMS、模组和pack,哪怕贴片线都是自己做,整个行业里面仅次于比亚迪。我下面用数据说话,这是第三方数据,零跑科技的pack、BMS装机量2022年4月份,pack在国内乘用车领域排名第五名,BMS排名第七名。作为做汽车的企业,能够在关键零部件领域排名行业前十,今年按20万台车的销售目标的话,电池产值会突破150亿。这是作为一家全域自研国内车厂,零跑汽车完全正向自主自研自制的成果。
再回到CTC的话题,CTC这两年非常热,大家提出了很多概念,很多厂商说我要做CTC。为什么进展比较慢?虽然讲是好讲,但是要跟整车结合,另外要把传统底盘和车身设计全部改掉,还是比较难的,它是一次尝试和挑战,是别人从来没有做过的事情,这也是零跑汽车的突破,是正向自研的成果。
零跑长期坚持全域自研、自主创新,行业有三家公司发布了相关技术,特斯拉、比亚迪和零跑。我们的区别在哪里呢?从我个人的经验来看,某家公司把车身集成到电池上盖,再加上把座椅安装结构做到电池上盖上,电池包还是独立体,只是省了车身的地板。包括B公司也是一样的,车身地板集成到电池包上,还是独立的电池包。零跑汽车更加创新,我们连电池包都没有了。为什么我们叫全球首个量产无电池包化?因为我们是把电池包大部分的结构做到了车身和底盘结构上,我们的电池包做出来不是完整的电池包,只有装在车上才是整体。当然,每条路线不一样,他们两家公司是我们学习的榜样,从这点来讲我们做得更彻底,我们的尝试更大胆。
关于可靠性,下面会讲到,我们做了四年的研发,做了两年半的测试。为什么能够说是全球首个量产无电池化,9月份我们的车型量产出来以后大家可以看看,跟他们两家公司不一样,他们有独立电池包,是传统的模式,只是把车的东西放在电池上。我们是完全改变,电池包独立出来是用不了的,只有装在车上才是电池包。CTC技术会加速电动产业链的重塑,开启电动新革命。
从CTC来讲,为什么说零跑智能动力CTC,加上了智能,因为电池包是硬件和软件的结合,只有硬件创新和软件创新才能持续OTA迭代,才可以变成有生命力的个体。
硬件创新,CTC电池包主要是两个创新,一个是底盘车身既是整车的结构又是电池包结构。第二个方面,怎么样解决气密性?很多人认为CTC气密性不好解决。我们为了做这个事情,四年前就把车身底盘全部改掉,不能按照传统的做,地板要做到绝对密封可靠,所有的骨架都要做到非常平整,通过改变传统车的结构设计来达到CTC密封的效果。我们用CTC双骨架环形结构,图片中红色是车身结构梁,绿色是电池托盘,绿色的梁这里也同时作为车身梁的部分结构,所以合二为一,做成完整的CTC结构,效果是使车身扭转刚度提升25%,整车轻量化系数相比用传统的电池包方案提高20%。
CTC技术带来的空间利用方面也非常好,我们把电池结构和车身底盘结构合二为一,很多的间隙就没有了,结构也可以省略掉,电池可用空间提升14.5%。传统电池包的安装间隙和上盖全部没有了,垂直空间省出10毫米。大家不要认为10毫米很少,微不足道,在车设计里面,哪怕0.1mm设计都很难,10毫米的空间是非常了不起的。基于此,在大家关心的综合续航能力和冬季续航能力都得到了提升,我们在相同轴距下有更好的空间,续航更长。我们的冬季保温性能是更好的,可以在车身底盘省出来的空间放防火保温棉,这个空间是有的。不但保护了电池的热失控,还起到保温作用,所以冬季的续航能力更好。第三季度量产的轿跑C01,纯电续航可以达到717公里。
说到电池性能,这里有实拍的视频,我们成立专门的CTC电池实验室,用四年的时间做这些工作。我们的CTC通过了30多项安全测试,专门对安全可靠性做了测试,特别是5米高空跌落,热失控扩散等远远超过国家标准。5米是什么意思?电池包装在车上,5米高空跌落在地上,不起火、不爆炸,没有一点问题。
从软件创新方面,我们研发了AIBMS,这是加上了车端和云端。传统都是从电芯的数据做算法,利用本车上BMS采集的数据做算法。现在采取云平台,以后车所有运行数据,通过运行数据做AI算法补偿,车开的时间越长,电池包的算法会更精准,容量状况和电池寿命可以计算更准确,这样才可以给客户带来更强寿命、更高安全。我们有安全监控算法,用解析模型算法加上故障解决,例如:在48小时甚至更长的时间,要发生安全事故了,可以提前2天报警,可以通知车辆返回检修,不用电池真的出故障再去检修。
我们可以称零跑CTC是可持续进化的能量母体,可以达到高适配,与整车匹配性高,可柔性化生产。这个结构不改变传统的冲焊涂工艺,只是在总装上稍微有点改变,所以对车间没有影响。另外,CTC也可以拆卸,电池出现故障的时候可以拆下来,不必要把车身座椅都拆掉。还有高度集成化、模块化,可跨平台接入各种车型。强扩展,我们用通用的热管理系统,加油式充电,充电5分钟续航200公里。
零跑CTC电池底盘一体化,通过勇于挑战自我的技术,可以给车子带来更长的续航里程和更强的安全性,这样的话可以跟其他公司一起引领CTC的发展。我们认为CTC技术应该是电动汽车的正确的发展方向,而且在今年4月份发布CTC技术的时候,朱江明董事长向外界公开,CTC技术可以免费开放共享。我们认为,技术不能成为壁垒,而应该成为推动整个行业发展的动力。一个人不能成就事业,需要大家一起推动,行业才可以得到发展,中国企业才可以走在世界的领先。
以上是我的演讲内容,谢谢大家。
(注:本文根据现场速记整理,未经演讲嘉宾审阅)