减少车身钢板厚度作为一个轻量化的有效手段被大家广泛吐槽,轰鸣君认为单单一个减少车身钢板厚度并不会让大家觉得偷工减料,毕竟群众的眼睛是雪亮的。但如果在减少钢板厚度之前考虑上成本问题的话,那确实槽点颇多。例如同样的车型,其中一辆把钢板做薄,节约了材料,节约了成本,但一旦出了事故,用户的第一感觉就是这辆车粗制滥造,偷工减料。
难道说轻量化就一定会使安全性下降吗?那要看减少的钢板厚度是不是减到了点子上,单从车身钢板的角度来讲,蒙皮钢板由于对车身安全起不到有效作用,所以对于这部分的“肥肉”而言,甩掉一部分反而更好,而发动机盖板上的蒙皮钢板更不宜过厚,过厚会影响到正面撞击时的溃缩吸能能力,反而会对乘员安全造成影响。
与减少蒙皮钢板厚度密切相关的另一个因素就是车身结构,在车身结构安全系数够高的前提下,蒙皮钢板厚度概念仿佛就显那么云淡风轻。
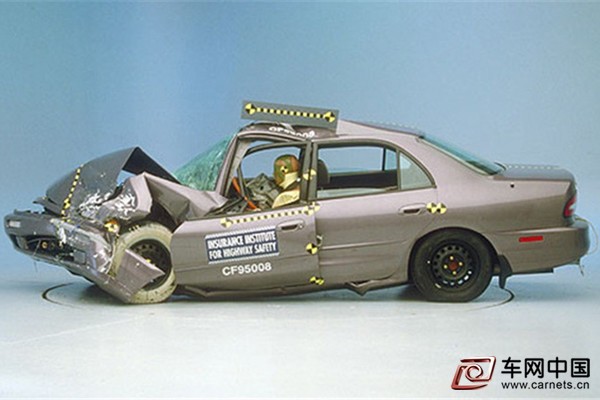
尽管车身强度主要取决于车身的结构设计,但在车身结构安全系数指标上依旧有厂家在玩文字游戏,材料的强度分为很多种,如屈服强度、抗拉强度、抗压强度、抗弯强度、抗剪强度、抗扭强度等,某些厂家宣称部分钢板的最高强度能够达到1600MPa,难道这车是潜水艇?要深海潜航?毕竟大气压强和深海水压完全不是一回事。
那这样的数据是从何而来?难道是造假?
在解释这个数据之前,轰鸣君先讲一讲原因,由于长久以来钢板厚度作为简单而直观的概念,在短时间内被大量接受,目前仍有不少人认为钢板厚就意味着皮实耐用,正是在这样的背景下,某些汽车厂商才玩起了“最高强度的游戏”。
话说回来,某些汽车厂商为了适应轻量化的趋势,又考虑到成本的因素,还要考虑到消费者的反应,就偷偷地把屈服强度和抗拉强度的概念进行了“偷梁换柱”,屈服强度反映的是材料抵抗永久变形的能力,抗拉强度反应的是材料抵抗断裂破坏的能力。举个例子,一根筷子想把它拉断很难(抗拉强度),但是把它折断就很简单(屈服强度),一般金属材料抗拉强度都比屈服强度高。
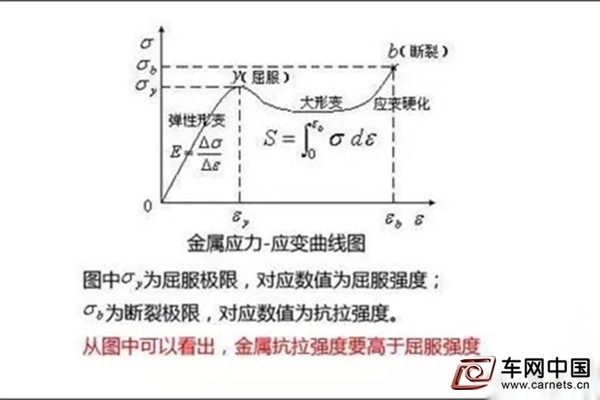
来点“实的”
要来实的那就需要资金的投入,从车身结构设计,受力分析计算,以及材料的选择进行投入,这些仅仅是科技上的部分投入,还有很大一部分是人力上的投入,这样的投入统统会计算到汽车的价格中。
一般为了安全性,乘员舱的骨架钢材一般都会选择强度较高的复合钢材,以防止事故发生时对乘员生存空间的挤压,如果还要兼顾到轻量化的因素,那就应该选择一些新型复合材料,或者是航空铝合金,这正是车身轻量化的“正道”。
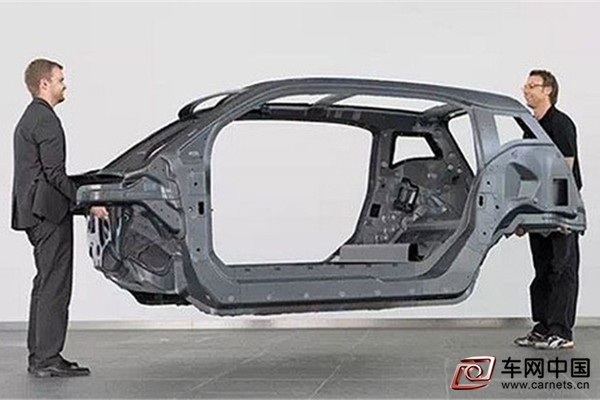
随着CAE技术的普及和进步,大量的优化方法被开发出来用于解决车身结构的优化设计,目前几乎所有的优化设计的思路都是在保持车身性能不下降的前提下降低车身重量。
与此同时,大量的新材料新工艺也在帮助车身降低重量。首先是高强钢,通过提升钢材的屈服强度,使同样结构设计的情况下,纵梁能吸收更多能量,A柱B柱不发生明显变形等等。现在屈服强度1000MPa的热成形钢已经普及了,未来屈服强度超过2000MPa的马氏体钢也已经开始了产业化。其次就是以铝为代表的轻质合金,采用铝合金可以显著的降低车身重量,代价就是成本比较高,目前还只在高端车身大量应用,10几万的车一般只有外覆盖件如发动机罩、侧门外板采用了铝合金材料。
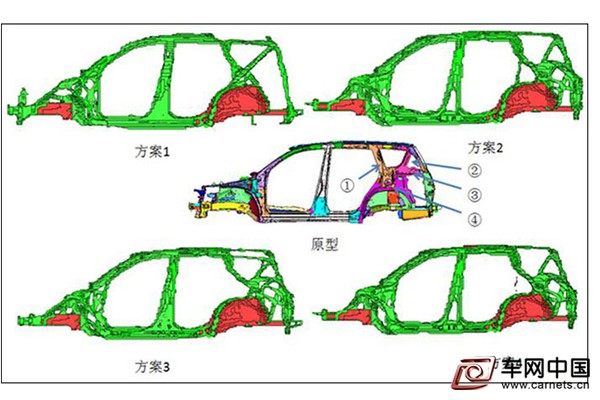
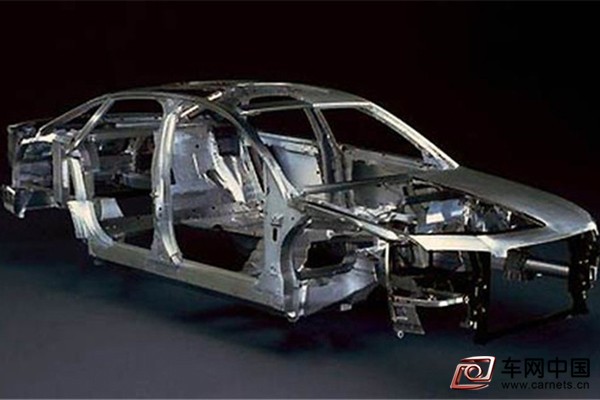
至此看来,轻量化和安全性并不冲突,由于目前技术的原因,造成了“长短脚”的情况。想要两手抓,那成本过高,单独抓其中一个又不符合现有的大环境,无论怎么选择,都是在跛着走路。如何根治掉“跛脚”的毛病,相信在竞争的压力下,未来的汽车会兼顾好轻量化和安全性之间的平衡。